Wilckens Yachtline - yacht paints and boat paints
Marine paints for boats and yachts a well proven range, for new boats and repairs
Products
- • Anticorrosive, primer, trowelling compounds
- • 1-component lacquer and 2-component lacquer
- • Antifouling
- • Wood protection
- • Thinner / others
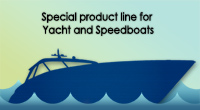
Steps to Successful Lacquering with Wilckens Yachtline
• Requirements
Yacht and boat coatings have to meet a host of different
requirements - they have to be suited to widely
differing construction materials, and they must
provide protection against numerous different factors.
Hence there is unfortunately no such thing as the
"ideal" coating material, applicable to every part
of a vessel, equally suited to every different construction
material.
Above the waterline coatings are subject to more intense sunlight and to splash water, below the water line coatings should, first and foremost, protect against fouling. Coatings also need to endure bottoming, or being dragged over gravely shores. In addition, sports and regatta vessels require a coating which is so smooth that only minimal surface resistance exists.
As can be seen, there are good reasons for choosing coating materials with properties which are specifically suited to the particular application in question
Furthermore, whether applying a first or second coating, or a refresher layer, following the correct working procedure is crucial. Make a note of all the steps necessary, and carefully read the corresponding system and product descriptions through thoroughly. Select the appropriate system and take particular note of the stated interval between coatings. One more tip regarding working practice:
Start off with stripping, cleaning and sanding work.AII surface preparations should be completed before applying any coatings.
Examine Existing Coatings
Where a repeat coating is being applied it is important to determine whether the existing coating is still properly bonded to the subsurface.
The degree of bonding can be tested easily using a highly adhesive strip. Press the adhesive strip onto various points on the surface to be coated, and then pull it off with a sharp jerk.
If old coating material sticks to the adhesive strip, the coating should definitely be removed otherwise successful bonding of the new coating is impossible. Former coatings can be removed by sanding or chemical stripper - the latter only for I -component products. Please note that old antifouling coatings should be removed with wet abrasive paper.
Basic rules for Re-coating
If the existing coating is in tact there are some important rules which should be followed:
• Where the composition or structure of a coating is unknown it is recommended that the coating be re-constructed from scratch. The chances of saving time and money by experimenting are slim, and the results usually unsatisfactory.
• Only apply a suitable new system to an existing coating.
Rule of thumb:
- Do not apply 2-component products to I-component under layers - unless this is specifically endorsed by the manufacturer.
- Self polishing or Teflon- (PTFE) based antifouling coatings can only be re-coated with the same material.
- When in doubt, contact the manufacturer directly.
Surface preparation
All surfaces to which a fresh coating is to be applied must be thoroughly cleaned beforehand. In particular dirt, oil, grease, wax, silicon, stripper or similar material must be thoroughly removed before commencement of sanding. Failure to due this will result in a spreading of the surface contaminants across the whole surface area through sanding dust. This applies equally to first coatings as to repeat coatings. Use special yacht cleaner, warm water and a brush, or a "Scotchbrite" sponge. It can be seen when the surface has been thoroughly cleaned as the water will run from the surface uniformly, without forming droplets.
In order to ensure optimal bonding of the new coating the surface should be well sanded, so that it appears uniformly dull. As dry sanding is usually a dusty business, wet sanding is recommended. This is also more economical as, providing it is keep sufficiently wet, the abrasive paper maintains its abrasiveness for longer. If dry sanding is favored nevertheless, it is advantageous to use a sander with vacuum exhaust attachment.
Important: always wear a dust and respiratory mask when dry sanding.
Which Abrasive Paper?
Dry Sanding Paper (corundum) | Wet Sanding Paper (silicon carbide) | |
Sanding color remnants following chemical stripping | 40-80 Do not dry sand antifouling |
40- 80 |
Sanding of filler | 60- 100 | 80- 120 |
Sanding of primer or antifouling | 100- 120 | 80- 120 |
Sanding of previously lacquered surfaces or gel coatings prior to are-coating | 120- 200 | 180- 240 |
Prior to minor repairs to a lacquer coating | 220- 400 | |
Sanding prior to final lacquer coating | 300- 400 | |
Prior to the polishing of 2-component lacquers | - 1200 |
Following sanding, the surface must be thoroughly cleaned again since sanding dust can adhere to it more firmly than one would expect. Rinsing with water, or removal with compressed air is often only partially effective. A thorough removal of sanding dust can only be achieved through a combination of brushing
and rinsing - hose in one hand, brush in the other. Re-rinse with ample fresh water.
Before coating can commence the surface must be absolutely dry.
Coating Thickness and Coverage
All Wilckens Yachtline products can be applied either with brush or roller. The surface area covered, as detailed in our product information is per coat, in the stated dry film thickness
However, a reduction of approx. 10 % should be expected when painting or rolling, or 30 % when spraying. Where thinner is used a greater surface area can be covered, however the film thickness of the coating once dry will be thinner accordingly.
Due to the variety of different types of yachts and boats there is no generally applicable formula for the calculation of the surface area below the water line. The following formula however provides a rough indication:
Length of water line x (width + draught)
- The surface area above the water line can be estimated with the formula:
2 x (overall length x middle freeboard) - For decks:
0.6 x (overall length x width) less area of cabin, cockpit etc. - For masts and spars:
Diameter x 3.14 x length
Paint Systems
Important Notes
• Drying Time
Drying time is highly temperature dependent whereby temperature refers to surface temperature during the drying process, Low temperature delays drying, higher temperature speeds up drying. Every 10°C increase in temperature will have a significant effect on drying time, The chemical curing of 2-component products usually requires a minimum curing temperature of
+ 10°C since the curing process draws to a halt at lower temperatures,
A second important factor in the drying process is the relative humidity, The higher the humidity, the longer drying will take, Relative humidity above 80 % is critical (surfaces can become matt, with the dew point being reached in localized points), Furthermore, air circulation and sunlight should also be taken into consideration. Since solvent vapors are heavier than air, when working in a closed room ensure good air circulation to avoid the slow drying and matt surfaces which vapors can cause, Otherwise, please refer to "Possible Dangers and Safety Tips"
• Dew Point
Dew and frost are well known, Their formation
is due to the different saturation levels of water in air at different temperatures (a cubic
meter of air can hold approx. I g of water at -
18°C, 5 g at 0 "C, 20 g at + 23°C and around 30
g at + 30°C),
When the maximum amount of water which can be held by the air at a given temperature is reached, the relative humidity is said to be 100 %. Cooler surfaces can become covered in a dew film, which can be invisible, brought about, for example, through wind, evening cooling, tanks being filled, drying rain, or through drying paint, For this reason it is usual practice only to carry out coating work when the temperature is at least 3 "C above the 'dew point (or at a maximum relative humidity of 80 %).
• Intervals Between Coats
For all 1- and 2-component products both a minimum and maximum must be closely adhered
to. The interval between coats is applicable not only to re-coating of the product with itself, and also to coating with further products. An "early" application of a further coat leads to solvent enclosure, resulting in deficient curing, In turn
this will cause blister formation when under water loading, "Late" application of the following coat hinders bonding with the new coat since, in the case of 2-component products, the material is already totally cured, Where the maximum interval between coats has been exceeded it is essential, also in the case of I-component products, that the surface be matt-sanded before the new coat is applied (ensuring the mechanical fixing of the newly applied coat).
System 1
Under water area (after surface preparation) 1-component products
POS | Product | Theoretical coverage ca. m²/l | Application method | Temperature at use/ of surface | Drying time at 20°C 80% rel. Humidity | Over coating Interval | Thinner/ Cleaner for tools | Recommended number of coats for different construction materials and special materials on board | |||||
Touch dry (hrs) | resistant against rain (hrs) | min. h | max. days | Fiberglass reinforced plastic | Wood, not Teak | Steel | Stainless, Steel, sea-water resistant Alu, | ||||||
1 | Universal primer | 11.5 | B/R/AS/LS | 5-30 | 1 | 6 | 16 | 90 | 1K | 2-6* ** | 4-5* | 2-6* | |
2 | Antifouling selfpolishing | 10.0 | B/R/AS/LS | 5-30 | 2 | 5 | 12 | 180 | 1K | 2 | 2 | 2 | |
* With airless spraying the double film thickness is possible. Then only 2-3 coats are necessary | |||||||||||||
** 6 coatings prevent osmosis on polyester | |||||||||||||
B= brush | LS= air-spraying | R= roller | AS= airless- spraying |
System 2
Under water area (after surface preparation) 2 component products
POS | Product | Theoretical coverage ca. m²/l | Application method | Temperature at use/ of surface | Drying time at 20°C 80% rel. Humidity | Over coating Interval | Thinner/ Cleaner for tools | Recommended number of coats for different construction materials and special materials on board | |||||
Touch dry (hrs) | resistant against rain (hrs) | min. h | max. days | Fiberglass reinforced plastic | Wood, not Teak | Steel | Stainless, Steel, sea-water resistant Alu, | ||||||
1 | Epoxyd primer | 16.0 | B/R/AS/LS | 10-30 | 2 | 5 | 16 | 7 | 2K | 3-5* ** | 4-5* | 5* | 2-6 |
2 | Antifouling selfpolishing | 10.0 | B/R/AS/LS | 5-30 | 2 | 5 | 12 | 180 | 1K | 2 | 2 | 2 | |
* With airless spraying the double film thickness is possible. Then only 2-3 coats are necessary | |||||||||||||
** 6 coatings prevent osmosis on polyester | |||||||||||||
B= brush | LS= air-spraying | R= roller | AS= airless- spraying |
System 3
Above water line colored (after surface preparation) 1 component products
POS | Product | Theoretical coverage ca. m²/l | Application method | Temperature at use/ of surface | Drying time at 20°C 80% rel. Humidity | Over coating Interval | Thinner/ Cleaner for tools | Recommended number of coats for different construction materials and special materials on board | |||||
Touch dry (hrs) | resistant against rain (hrs) | min. h | max. days | Fiberglass reinforced plastic | Wood, not Teak | Steel | Stainless, Steel, sea-water resistant Alu, | ||||||
1 | Universal Primer | 11.5 | B/R/AS/LS | 5-30 | 1 | 6 | 16 | 90 | 1K | 2 | 2 | ||
2 | Yacht-Vorlack | 11.0 | B/R/AS/LS | 5-30 | 1 | 5 | 16 | 90 | 1K | 1 | 1-2 | 1 | |
3 | Super Lacquer | 10.0 | B/R/AS/LS | 5-30 | 3 | 10 | 16 | 90 | 1K | 1-2 | 2-3 | 1-2 |
System 4
Above water line colored (after surface preparation) 2 component products
POS | Product | Theoretical coverage ca. m²/l | Application method | Temperature at use/ of surface | Drying time at 20°C 80% rel. Humidity | Over coating Interval | Thinner/ Cleaner for tools | Recommended number of coats for different construction materials and special materials on board | |||||
Touch dry (hrs) | resistant against rain (hrs) | min. h | max. days | Fiberglass reinforced plastic | Wood, not Teak | Steel | Stainless, Steel, sea-water resistant Alu, | ||||||
1 | Epoxy Primer | 16 | B/R/AS/LS | 10-30 | 2 | 5 | 16 | 7 | 2K | 2-3 | 2-3 | 2-3 | 2-3 |
2 | DD-hard lacquer | 10.5 | B/LS | 10-25 | 1 | 4 | 8 | 2 | 2K | 1-2 | 2-3 | 1-2 | 1-2 |
Systematic protection of Wood
The lacquering and renovation of yachts and boats of wooden construction is one of the most satisfying jobs of all, providing a real feeling of achievement. The result of a good lacquer coating is immediately visible, and the lengthy preparations soon forgotten.
But a lacquer coating not only brings out the natural beauty of wood, but also ensures the value of the ship almost indefinitely - with minimal effort and expense. Using our coating system - specially developed for all types of wood used in boat construction - annual overhauling work is kept to a minimum. With correct application of the product, the time taken will hardly be more than that necessary for a boat constructed of glass fibre reinforced plastic
Even when it sometimes appears to be the case, the correct use of a brush and lacquer is easy enough. Inexperienced lacquerers can achieve good results in a relatively short period of time - providing the following simple, but important guidelines are followed. Even the best lacquer will, in the long term, not bond with a poorly prepared surface
Hence the first rule:
- The better the subsurface, the longer the lacquer will hold, and the better the wooden surface will look .
- Never paint directly from the tin:
It is inevitable that dust particles will be transferred via the brush into the lacquer. For this reason it is recommended that the approximate volume of lacquer required be poured into an additional container. One of the secrets of a good surface is a thin application. - For this reason many thin layers are recommended, rather than fewer thicker layers. Where lacquer is applied too thickly it will not harden properly, which can lead to surface wrinkling, "tears" (droplets) or ridges which will have to be laboriously sanded down next year.
System 5
Wood Protection above water line and inside clear (after surface preparation)
POS | Product | Theoretical coverage ca. m²/l | Application method | Temperature at use/ of surface | Drying time at 20°C 80% rel. Humidity | Over coating Interval | Thinner/ Cleaner for tools | Recommended number of coats for different types of boat construction wood | |||||
Touch dry (hrs) | resistant against rain (hrs) | min. h | max. days | Conifers | Hard wood Oregon, oak, ash tree | Tropical wood Teak Mahogany | Water resistant glued ply-wood | ||||||
1 | Yacht Lacquer* | 10.5 | B/AS/LS | 10-30 | 3 | 16 | 24 | 90 | 1K | 5* | 5* | 5* | |
Alternative to Pos.1: DD-hard lacquer | 12.5 | B/AS/LS | 10-30 | 1 | 4 | 8 | 2 | 2K | 5* | 5* | 5* | 5* | |
* 1st coat with 30%- 40% added thinner | |||||||||||||
2nd coat with 10%- 20% added thinner; after the first coat the upright standing gravis are sanded | |||||||||||||
B= brush | LS= air-spraying | R= roller | AS= airless- spraying |
System 6
Wood Protection solid woods below the water line, e.g. oak, teak and
mahogany (after surface preparation)
POS | Product | Theoretical coverage ca. m²/l | Application method | Temperature at use/ of surface | Drying time at 20°C 80% rel. Humidity | Over coating Interval | Thinner/ Cleaner for tools | Remarks | |||||
Touch dry (hrs) | resistant against rain (hrs) | min. h | max. days | ||||||||||
1 | 2K- Thinner | 10.0 | B | 5-30 | - | - | After drying | - | Wash out natural elements, allow to dry | ||||
2 | DD- Hard Lacquer with 30% 2K- Thinner | 9.0 | B/AS/LS | 10-30 | 1 | 4 | 8 | 2 | 2K | Apply 1 coat as bonding layer | |||
3 | CR universal primer | 11.0 | B/R/AS/LS | 5-30 | 1 | 6 | 16 | 90 | 1K | 4-5 coats | |||
4 | Antifouling Selfpolishing | 10.0 | B/R/AS/LS | 5-30 | 2 | 5 | 12 | 180 | 1K | 2 coats | |||
B= brush | LS= air-spraying | R= roller | AS= airless- spraying |
Treatment of Teak Decks
In bygone years it was generally sufficient to scrub down a teak deck with green soap every now and again. This would lend the wood a beautiful white grey tone which would protect the surface from the elements like a patina. Sadly this is no longer sufficient. The wood needs protection from aggressive industrial emissions, otherwise dirt will penetrate too deeply to be removed, damaging the wood, particularly between the grain
The products Teak Cleaner, Teak Refreshner and Teak Sealer provide long-term protection against the harmful effects of air pollution, and restore and maintain the wood's natural beauty. The simplest method to get strongly soiled and old grayed teak wood clean:
• The teak deck is soaked thoroughly with a lot of water (excess water has to be removed with a cloth).
• Apply cleaner with a soft brush evenly and saturated to the damp teak area. After this the complete surface is worked on thoroughly with a hard brush or scrubbing brush. The damp surface must not
be allowed to dray during this process.
• Then the area must be flooded with a lot of fresh water and excess water removed with a clean cloth. The damp area has to be treated with Teak - Refreshner. Teak - Refreshner is applied with a soft brush evenly and saturated. After a few minutes the teak area can be rinsed with a lot of fresh water. After thorough drying the treated teak wood should be sealed with Teak - Sealer.
Further Benefits:
• Following thorough treatment with Golden Teak only minimal maintenance is necessary as the penetration of dust and aggressive dirt into the wood is hindered.
• In contrast to oil treatment, the deck remains non-slip.
• Preservation of the wood reduces wear; the surface is physically protected.
System 7
Teak Decks
POS | Product | Theoretical coverage ca. m²/l | Application method | Temperature at use/ of surface | Drying time at 20°C 80% rel. Humidity | Over coating Interval | Thinner/ Cleaner for tools | Remarks | |||||
Touch dry (hrs) | resistant against rain (hrs) | min. h | max. days | ||||||||||
1 | Teak- Cleaner | 4.0 | B | - | - | wet in wet | 1K | Wash with plenty of water | |||||
2 | Teak- Refreshener | 4.0 | B | - | - | After drying | 1K | after 10 min. absorbsion wash with plenty of water | |||||
3 | Teak- Sealer | 9.0 | B | 10-30 | 1 | 3 | 3 | 1 | 1-2K | Only use thinner for cleaning tools | |||
B= brush |
Fibre Glass Reinforced Plastic/ Osmosis Damage in Polyester
"Real" osmosis is to be understood as contact surface blisters formed between the gel coat and laminate, or within the laminate, containing a liquid which is reactive to acids.
I n assessing the extent of the damage the following factors are important:
• Quantity, size, local distribution and pattern of the blisters.
• Affected areas (as a percentage), delamination, and whether mechanical stability is still ensured.
The following have come to be recognized as causes of "real" osmosis:
• Gel coat is too thin or micro porous, or too highly filled
• Air voids
• Insufficient hardening or preparation
• Hydrolysis
• Ageing
• Natural diffusion of water
• Damage due to chlorinated hydrocarbons such as methylene chloride, dichloromethane and trichloroethane.
System 8
Treatment of Osmosis
POS | Product | Theoretical coverage ca. m²/l | Application method | Temp at use/ of surface | Drying time at 20°C 80% rel. Humidity | Over coating Interval | Thinner Cleaner for tools | Recomm. number of coats | Remarks | |||||
Touch dry (hrs) | resistant against rain (hrs) | min. h | max. days | |||||||||||
1 | Epoxy primer | 16.0 | B/R/AS/LS | 10-30 | 2 | 5 | 16 | 7 | 2K | 1 | ||||
1a | Only if constructional stability has to be restored: Epoxy-Resin | Aprox. 1kg per 500g glass | B/R | 10-30 | 1 | 3 | 3 | 1** | *** | 2-3 | In accordance with construction calculations the necessary layer(s) of glass laminate are applied wet on wet. CARE' Only use glass for use with epoxy-suited skims | |||
2 | Epoxid-Feinspachtel (up to I mm depth of layer per layer) | As required | Filling knife | 10-30 | 3-4* | No | 6 | 1** | *** | As required | Fill holes and bubbles up to a max layer thickness of 3 mm (three working steps) | |||
3 | Epoxid Feinspachtel | 1 | Filling knife | 10-30 | 3-4* | No | 6 | 1** | *** | Apply material with smoothing trowel or filling knife. Sand the whole area. Repeat as necessary until a smooth surface is achieved | ||||
4 | Epoxy Primer | 16.0 | B/R/AS/LS | 10-30 | 2 | 5 | 16 | 7 | 2K | 1-3 | ||||
5 | Antifouling selfpolishing | 10.0 | B/R/AS/LS | 5-30 | 2 | 5 | 12 | 180 | 1K | 2 | ||||
The damaged gel coat and laminate must be thoroughly removed. Suitable methods include sandblasting or rasping. Thereafter a thorough washing with high pressure water at a nozzle distance of approx. 10 em is necessary in order to remove all traces of salts and decomposition products. The following thorough drying out is particularly critical. It is recommended that the boat be enclosed, and drying aids employed, such as a dehumidifier. The surface must be free of loose particles, dust and grease. Where large areas of delaminating have occurred it should be determined whether constructional stability is still ensured. and precautions taken accordingly. | ||||||||||||||
* sandable | **must be followed by sanding | ***only use for cleaning tools |
The product labelling will indicate whether any of the substances mentioned above, which would be damaging to GFRP materials, are contained in the product. To avoid a re-occurrence of "real" osmosis,
yachts and boats, whether new or in use, should be preserved with a preventative coating of epoxy primer of the recommended film thikkness.
Filling works
The success of any filling work is generally dependent on a number of factors:
• The size of the area to be filled
• Subsurface / material
• Subsurface preparation
• Correct choice of suitable filler tool (we highly recommend our epoxy filler tool)
GFRp, steel and aluminum should be well cleaned and free of grease. After sanding but before filling, a layer of epoxy primer should be applied. Then apply the chosen coating system in accordance with the corresponding instructions
Try to avoid filling work on wooden constructions. Should smaller areas require filling, the following points should be noted:
Nordic woods should be well-sanded and dust free before application of filler directly to the wood. Hard woods and tropical woods should be washed with 2K-thinner to remove natural elements before sanding and removal of dust. Small areas can then be repaired.
Then apply the chosen coating system in accordance with the corresponding instructions